Ebo Systems a inauguré sa nouvelle presse de 1200 tonnes et l’extension du bâtiment
Ebo Systems a développé en 2013 un concept de Chambre De Tirage, qui a donné lieu à différentes étapes dont la première était les calculs en recherche et développement pour estimer ses capacités techniques (la validation numérique a duré environ 2 ans), parallèlement une étude de marché a été menée en consultant les offres de la concurrence, celle-ci a révélé un potentiel de 150 M€ pour le marché européen et surtout un marché de type monopole puisque occupé quasiment par un seul confrère.
Le contexte
La société a donc décidé de rentrer sur ce marché puisqu’elle avait connaissance du composite et qu’elle voulait se diriger vers des produits haut de gamme : des poids de tenues selon la norme EN 124 (B125 à D400). Elle a déterminé le créneau, les segmentations du marché, fait une étude du prix global de revient et du prix de vente potentiel.
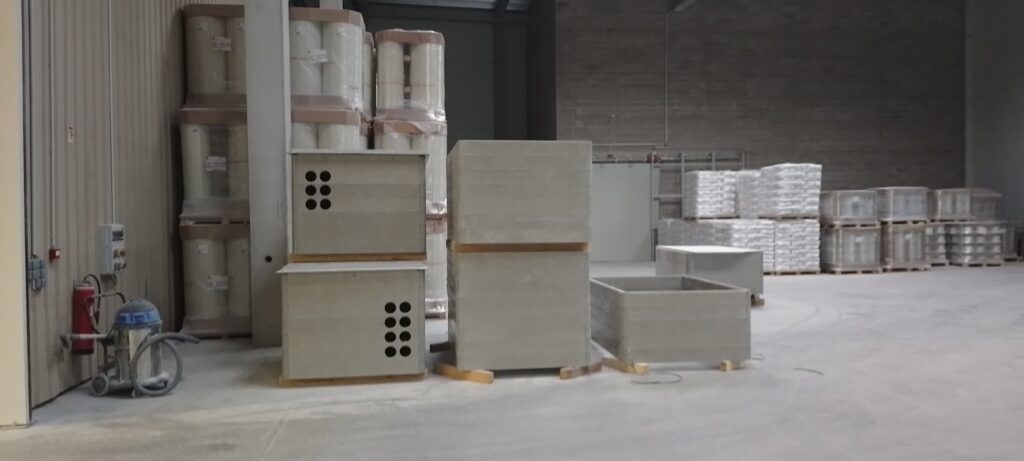
Cette phase d’étude technique (donc théorique) terminée, Ebo Systems a commencé à développer concrètement son concept, une filière de pultrusion a été conçue, un outillage pour faire les angles a été fabriqué, des sous traitants ont réalisés des prototypes de cadres en métal galvanisé à chaud et d’autres de la filière composite ont produits des dalles en PRV de classe B125, tout réuni Ebo s’est équipé pour faire les premiers tests.
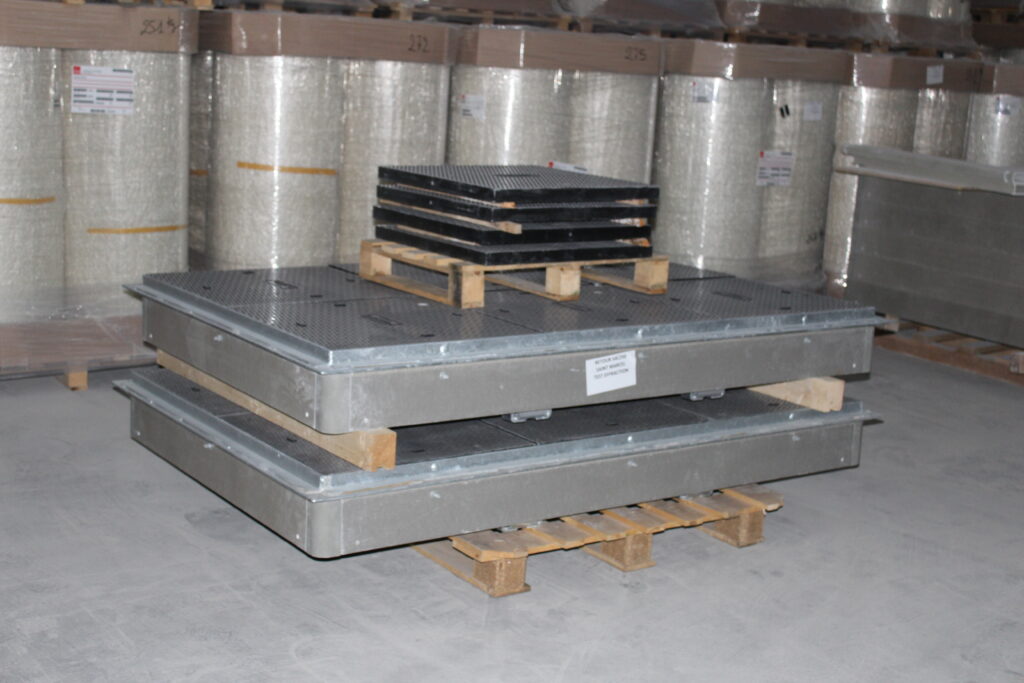
En 2015, estimant être prêt Ebo Systems a répondu à un appel d’offre émis tous les 4 ans par la SNCF, le projet a été pré validé techniquement mais l’offre était 15 à 20 % plus élevée que celle de la concurrence.
Souhaitant faire une nouvelle offre en 2019, la société « a entièrement revu sa copie » pour devenir compétitif et avoir un prix concurrentiel, sachant que son concurrent est établi sur ce marché depuis plus de 25 ans, qu’il dispose d’une grande expérience et d’un amortissement clos de ses machines et outillages.
Ebo Systems a travaillé sur 3 thèmes :
- Le coût des couronnes, la RDI a développé un système de clipsage
- Les cadres, trouver des solutions technico économiques pour baisser les coûts tout en gardant les résistances mécaniques nécessaires
- Intégrer dans sa production les dalles.
Frédéric Brandquien en novembre 2020, après avoir préparé le dossier d’investissement décroche le contrat cadre de la SNCF pour les 4 à 6 années suivantes, ce qui lui indique que l’offre est inférieure à celle de la concurrence.
Cette réussite déclenche une série de besoins immédiats pour la fabrication des dalles : place, machines, outillage …, il va falloir donc investir environ 1,5 M €, des heures de travail…, cet investissement sera pour un nouveau bâtiment, une presse de 1200 tonnes, et un nouvel outillage. Il devrait générer un CA de 5 à 6 M€/an.
Deux actions sont mises en place :
- La construction du bâtiment et l’établissement d’un process de production
- La validation définitive des chambres de tirages, le coût est élevé car les tests réalisés en internes doivent être confirmés par des laboratoires d’essais extérieurs indépendants ou des laboratoires de la SNCF
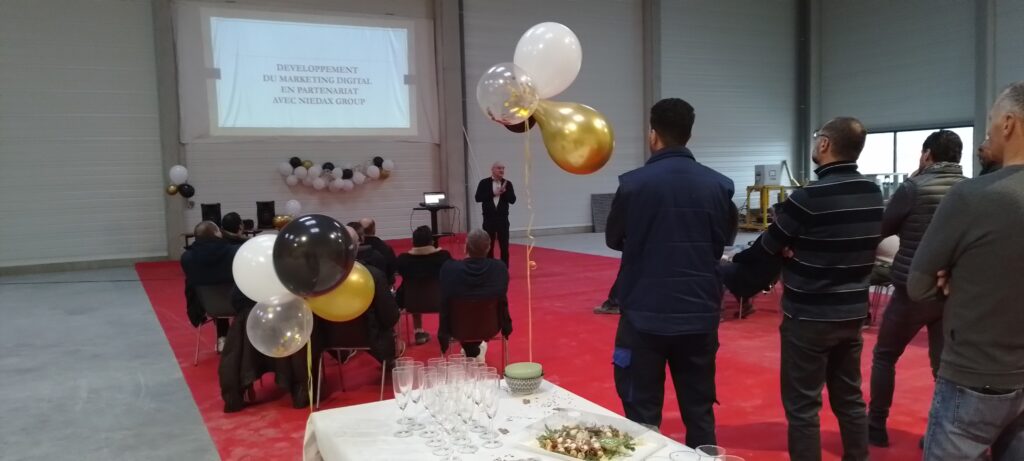
En 2022 des chantiers tests de la SNCF ont mis à l’épreuve pour une durée d’un an, les produits proposés en termes de géométrie, de mise en œuvre et de résistance.
La SNCF est une étape nécessaire mais pas suffisante, elle couvrira environ 50% de l’outil de production, la société a identifié d’autres centres d’intérêt notamment dans l’eau, stations d’épuration, traitement des eaux…, elle est approchée par des clients qui veulent :
- Trouver une alternative pour sortir d’un monopole tenu par une entreprise sortie de l’Union européenne qui a une politique de prix élevée,
- Parvenir à une baisse des coûts de transports,
- Obtenir une grosse réactivité dès la validation des commandes.
L’appartenance au groupe Niedax et l’implantation géographiques des filiales permettent également d’ouvrir dans un premier temps le marché européen à l’usine Ebo Systems implantée à Villers-La-Montagne (54).
Les chambres de tirages de la firme ont de plus l’avantage, par rapport à leurs concurrentes, de pouvoir être conçue en sur mesure, elles ne sont pas soumises à des dimensions de moules, donc le passage du standard au hors standard est plus aisé. Et le procédé a été validé par la SNCF.
La nouvelle PU7 montre dans ce contexte sa nécessité car elle seule permet de produire en 2 empreintes les profils de chambres de tirages, elle va désengorger les lignes et fabriquer des profilés plus gros. Elle va devenir également l’élément central pour le prochain projet stratégique d’Ebo Systems, qui est l’augmentation de la part de marché du caniveau composite.
Le plan d’action
Un plan d’actions nommé : développement investissement, industrialisation des chambres de tirage conformes au cahier des charges en quantité et prix de revient correspondant au contrat SNCF, a été établi afin de déterminer l’ensemble des tâches, le responsable de chacune, l’équipe affectée à celle-ci, une date de début et une date de fin.
7 étapes ont été reconnues lors de l’étude préliminaire :
- Obtention de la validation de commande, accord Niedax groupe pour investissement,
- Mise en place d’une politique marketing, commerciale,
- Négociation achats de matières premières, mise en place d’ordonnancement, définition du stockage, chargement, transport,
- Définition du concept industriel au niveau des bâtiments, machines et réalisation de l’outillage,
- Définition de produits process pour la production de chambres de tirages,
- Contrôle de rentabilité (objectif diminuer ou maitriser les coûts de revient),
- Validation, suivi de production, produits de process qualité, environnement interne et externe clients groupe Niedax.
La presse de 1 200 tonnes
Lors de l’achat de la presse, 3 solutions se sont présentées. La première est une presse Italienne dont le prix était assez élevé. La 2e était une presse allemande, déjà exploitée en République Tchèque, et à laquelle Ebo portait un énorme intérêt. Seulement, il s’est avéré qu’un énorme travail de mise à niveau était nécessaire. La 3e était l’entreprise Pinette, qui a fait une première offre dans l’enveloppe de celle des Italiens.
La société Pinette, installée à Chalons -sur -Saône, a ouvert à une délégation de la société Ebo Systems les portes de son usine, et la conduite sur plusieurs sites de ses clients de très longue date où elle a pu voir à l’ouvrage ses machines. La société Ebo Systems s’est entretenue avec certains de ses confrères qui produisent de très grosses pièces en SMC (mélange de résine, de charges inertes, de fibres…), et a vu la conception de nouvelles presses. La société Pinette a ensuite fait une nouvelle offre avec un prix nettement revue à la baisse. Pour Ebo Systems travailler avec une entreprise française comme Pinette ne présentait que des avantages en termes de programmations, de langage, de rapidité pour la prise de décisions (les deux parties ont été réactives et en bonne entente). Monsieur Brandquien estime qu’il a reçu un bon produit, sur mesure, clé en main, installé et mis en route.
Plusieurs éléments ont dû être pris en compte comme l’encombrement, un toit à 14 m n’était pas envisageable, une fosse a été exécutée afin que le plateau soit au raz du sol, ce qui était également un souhait.
Entretien avec Franck Dantigny de Pinette PEI (18.11.21)
Fonction : Metteur au point depuis 21 ans au sein de Pinette, société implantée à Châlons-sur-Saône, spécialisé dans le montage et dans la mise en route de ce type de machines sur site, surtout le grand export.
Présentation de la société : Pinette fabrique en particulier de la presse hydraulique, construit des lignes automatiques et livre des usines clé en main. Toutes les machines sont faites sur mesure.
La particularité de la presse d’Ebo Systems est qu’elle travaille avec 4 vérins qui fonctionnent en diagonale, car deux vérins de fort tonnage sont activés à la fermeture pour exercer une forte pression sur le moule, mais la société a besoin de pression non négligeable à l’ouverture, ainsi 2 vérins travaillent pour ouvrir la presse. Sa capacité est de 1200 t, elle est équipée d’une imposante rampe d’accumulateurs à azote afin d’atteindre une vitesse rapide à la fermeture.
La machine pèse 46 tonnes, elle atteint les 55 tonnes avec son équipement complet.
La presse a été commandée en avril 2021, elle est installée en novembre 2021, après 6 mois de fabrication. L’étude et la construction complète, découpe, usinage, ont été exécutées au sein de l’usine de Châlons.
- Pour l’étude ont travaillé 1 ingénieur hydraulique, 1 ingénieur électricien, 1 ingénieur pour le schéma et le choix des composants, 2 techniciens ingénieur mécanique pour la conception globale de la machine, 1 chef de projet.
- Pour la fabrication ont travaillé 2 chaudronniers, 2 usineurs, 2 électriciens, 2 tuyauteurs et 3 monteurs pour l’assemblage en atelier. La presse a été testée pendant 2 semaines.
- 2 personnes sont occupées au montage sur site.
Fiche d’identité du chantier
Maîtrise d’œuvre
Architecture | EGG Architecture |
Contrôle technique | Apave |
Études et maitre d’œuvre | Racine |
Ingénierie conseil de la construction | Fondasol |
Corps de métiers pour le bâtiment
Investissement global environ 800 000 €
Terrassement – VRD | Colle TP |
Démolitions – Gros Œuvre | Réato |
Charpente beton | IDB |
Charpente métallique | ACMT/Valtefogle |
Étanchéité – Bardage | FACE/ACMT |
Dallage | Placeo |
Serrurerie | Manuregion /Frechin |
Électricité / Fluides / Installation sprinklage | Racine |
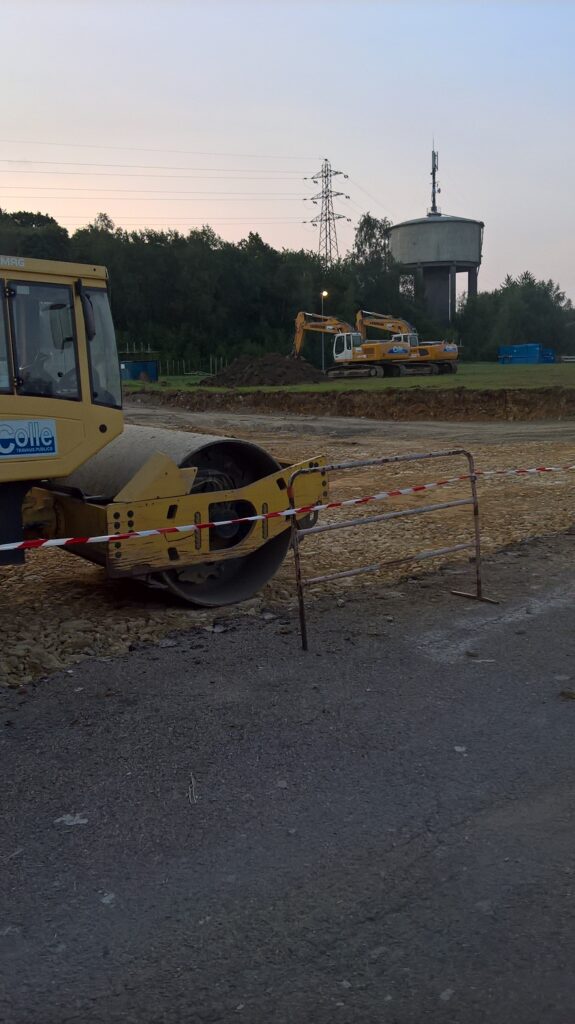
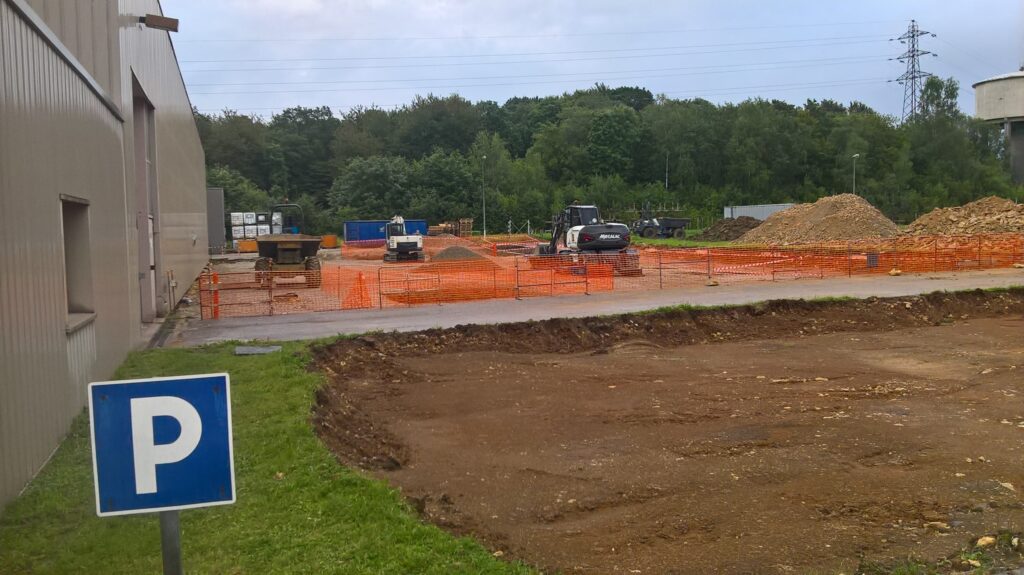
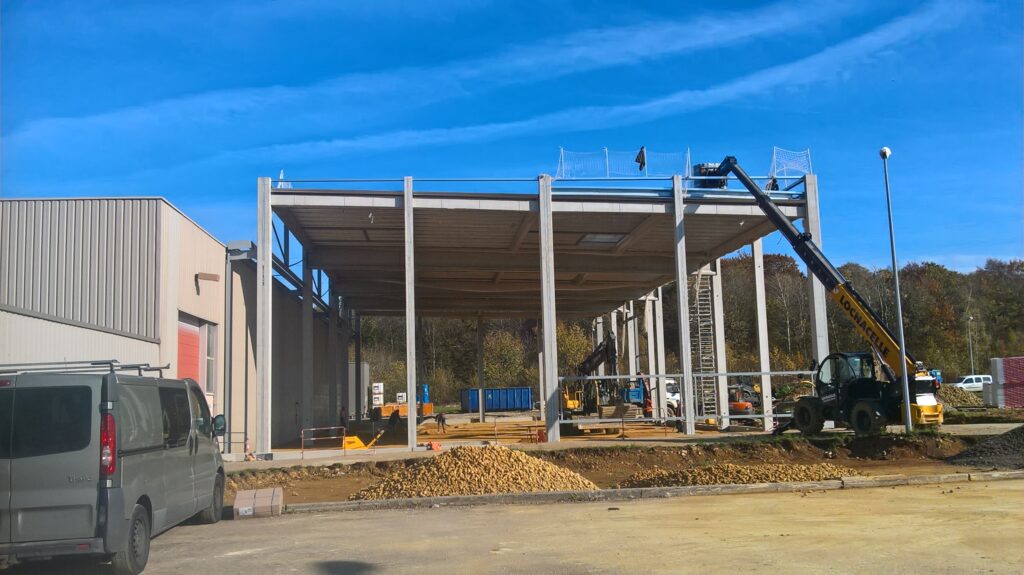
Corps de métiers pour la zone presse
Investissement global environ 700 000 €
Presse 1200 tonnes | Pinette PEI |
Réchauffeur et refroidisseur d’huile | FIT Plasturgie |
Moule outillage dalle PRV | M2PI |
Moule doublage CTB | DMM |
Filière de pultrusion incluant modifications | LUM |
Filière profilé renfort | LUM |
Moule renfort CIN | DMM |
Machine d’assemblage | Ebo Systems |
Enclume et conformateur | Ebo Systems |
Adaptation PU7 pour Chambre De Tirage | INOV |
Modification programme | INOV |
Levage, manutention | Lorlev, filiale de Mediaco, mise à disposition de 2 grues Liebherr, une de 160 t + 50t de contrepoids et une de 60 t, effectif 6 personnes. |
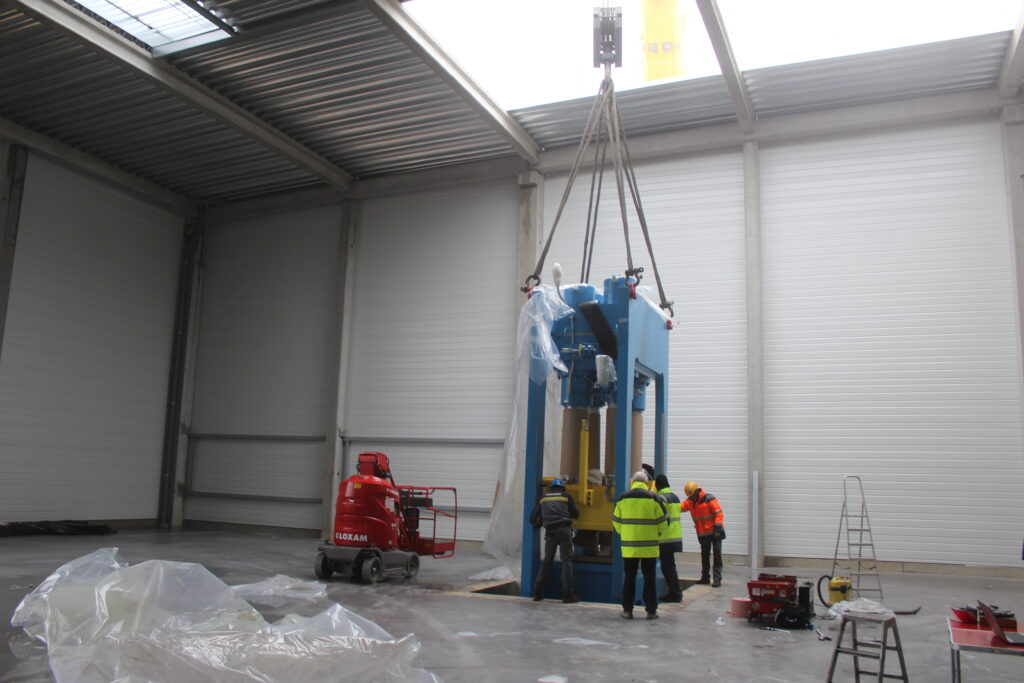
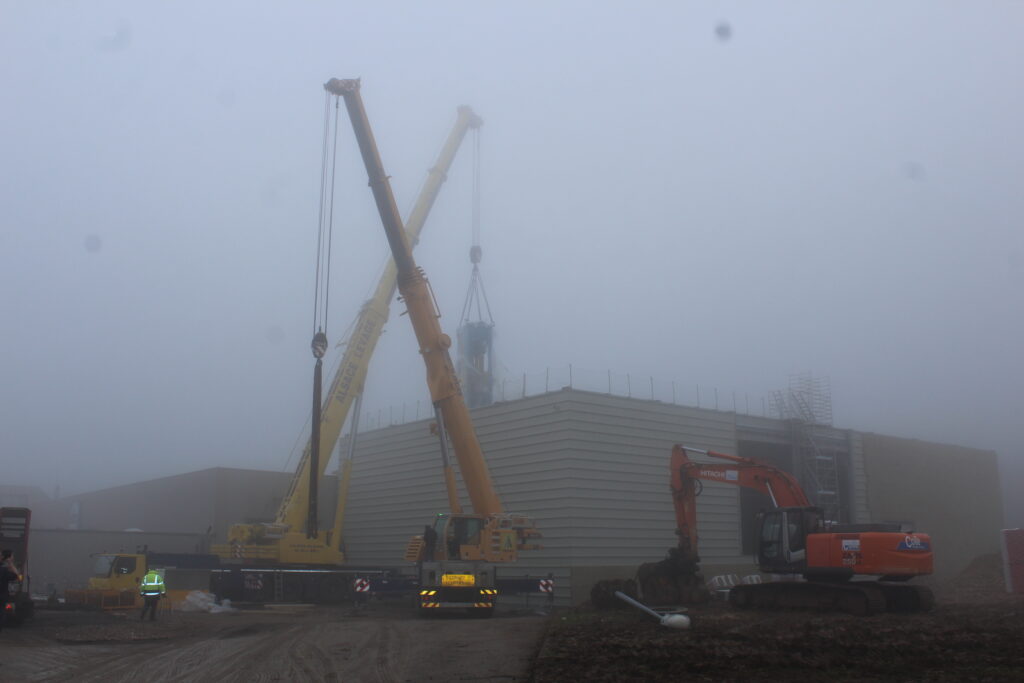

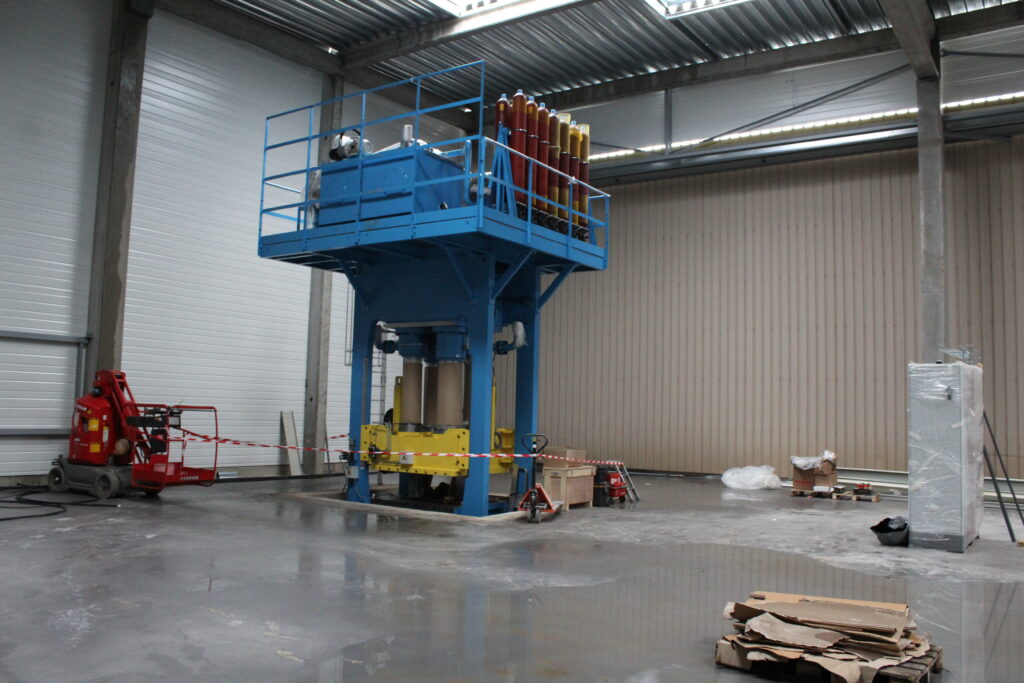